15kg High Torque SCS215 Serial Bus Servo with Beautiful Wiring
Specifications
- Dimensions : 45.2*24.7*35mm
- Weight : 50g
- Operating Angle : 0-180 Degree
- Bus Interface : TTL Level Multi Drop
- Control Type : Bus Packet Communication
- Control Protocol : Half Duplex Asynchronous Serial Communication
- Servo ID available : 0 - 253
- Communication Speed : 38400 bps - 1M bps
- Feedback Type : Position, Temperature, Load, Speed, Voltage
- Operating Voltage : 4.8V - 7.4V
- Stall Torque (Kg.cm) : 17 (4.8V) - 19.5 (7.4V)
- Stall Current : 1.5A (7.4V)
- Speed (RPM) : 0.18 sec/60° (6V) - 0.15 sec/60°(8.4V)
The advantage of Serial bus servo:
1.Beautiful wiring structure,
2.Easy to control signal,
3.real-time feedback of position,tempreture,speed,voltage,Current data,
4.Less occupied port.
5.Digital transmission signal is
Flexible, convenient, reliable and good compatibility
6.intercommunication;
Now PWM is Simulate Transmission,Pulse width variation stand for control vector,so easily interfered by the outside world.
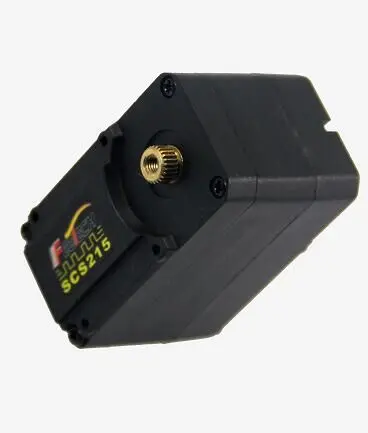
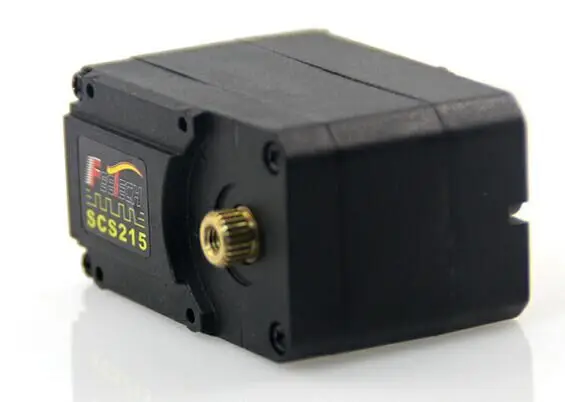
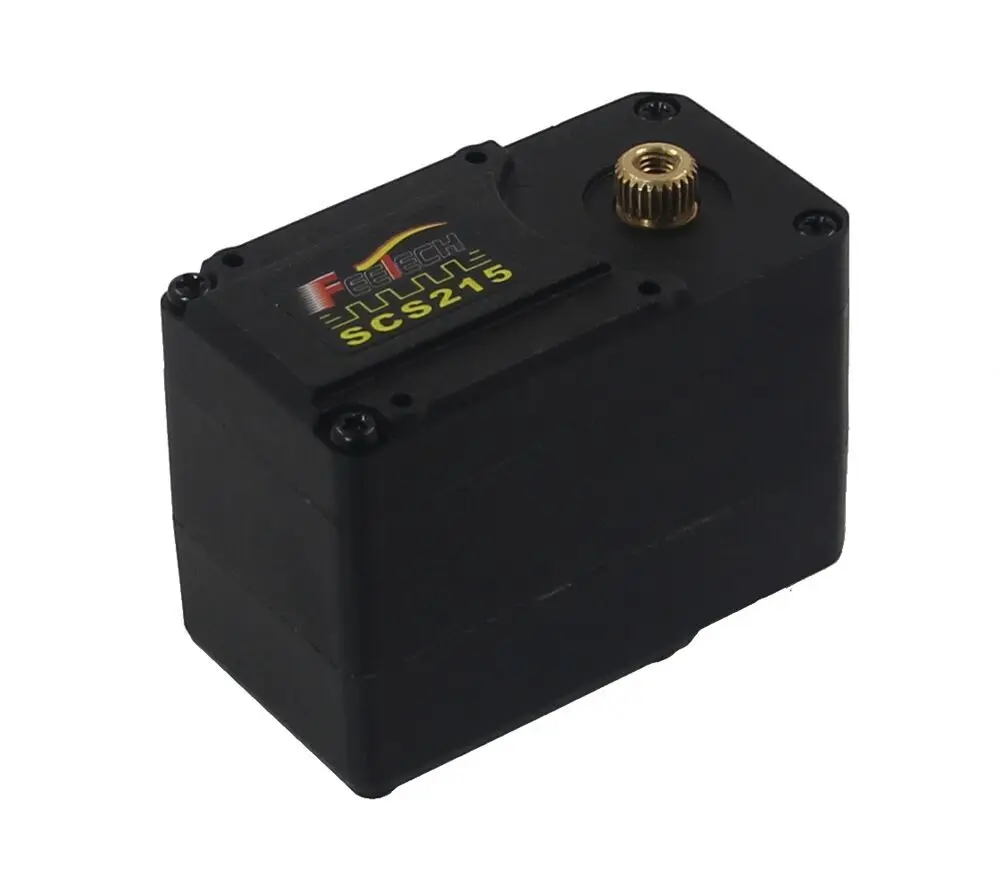
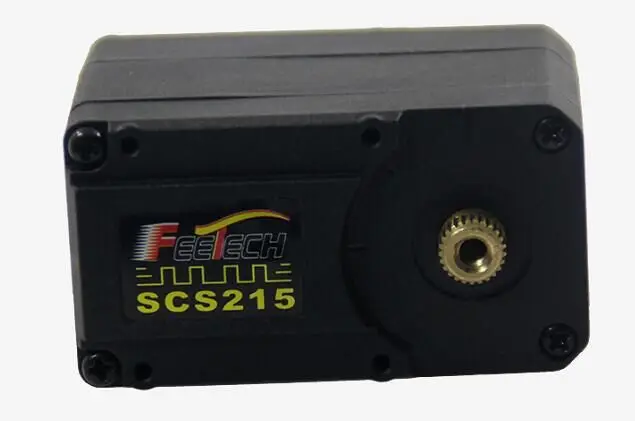
it is daisy chained servos, has feedback, etc... However, the SCS215 comes with brackets, horns, etc...
The SCS215 high torque (19.5 kg.cm max) robot servo has the ability to track its speed, temperature, shaft position, voltage, and load. The servo can be configure as positional or continuous rotation mode. The control algorithm used to maintain shaft position on the SCS215 robot servo can be adjusted individually for each servo, allowing you to control the speed and strength of the motor's response. All of the sensor management and position control is handled by the servo's built-in microcontroller. This distributed approach leaves your main controller free to perform other functions.
The SCS215 robot servo is a Serially Controlled servo that provides commands and feedback parameters to allow complete control over your robot application. The Serial protocol is daisy chained, meaning several servos can be connected to each other in a chain and offer several compliance and sensing parameters that can be configured and read including position, velocity and temperature.
The SCS215 smart control servo use special half-duplex UART bus as input source. User need to use a SCPC-2 programmer to configure the smart control servos using PC via USB port, or make a TTL linker circuit to communicate to other host MCU.
You can use Arduino to control SCServo. You will need a TTLinker connected between Arduino and SCServo.
TTLinker is a signal conversion board. Arduino needs to convert its UART signals to the half duplex type and through TTLinker connect to SCServo.
Feature:
SCServo can work at servo mode and wheel mode.
The servo mode can be used to multi-joints robot since the robots can be controlled with specific angles. (The factory default setting is servo mode)
The wheel mode can be used to wheel-type operation robots since motors of the robots spin infinitely. (If wheel mode is available you need to program the value of position limitation the both are 0.)
If you want to reprogram servo, you need to download the PC software (SCServo_Debug), and to connect SCPC-2(Serial Control Programming Card) between servo and PC.
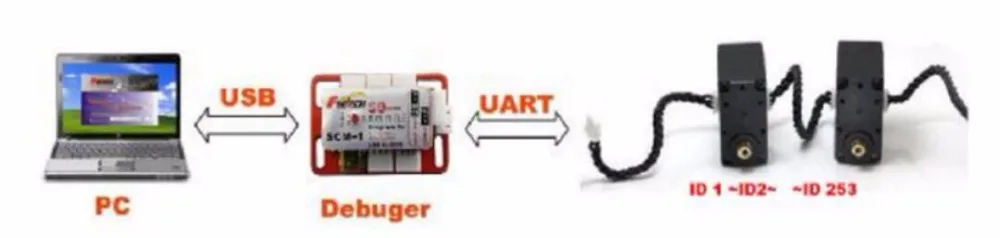
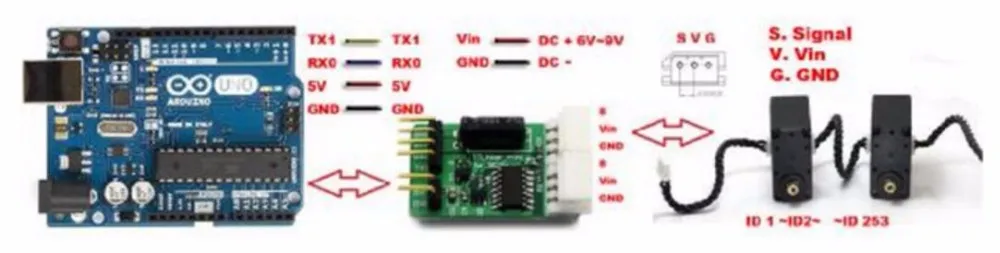
Full Packaged
-Servo×1PCS
-Servo arm×1 bag
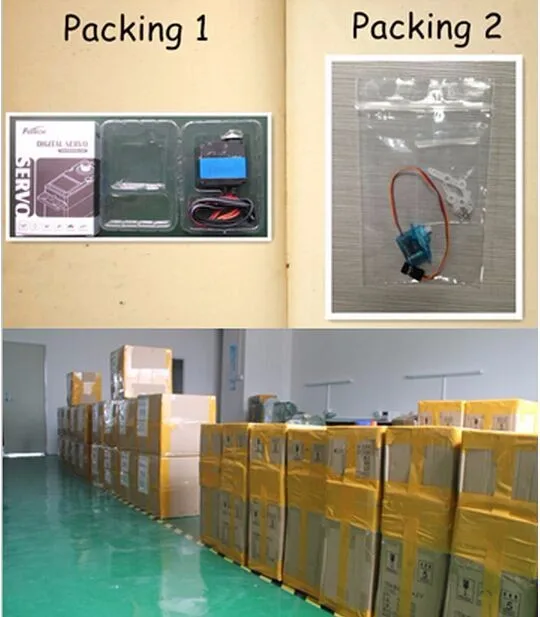